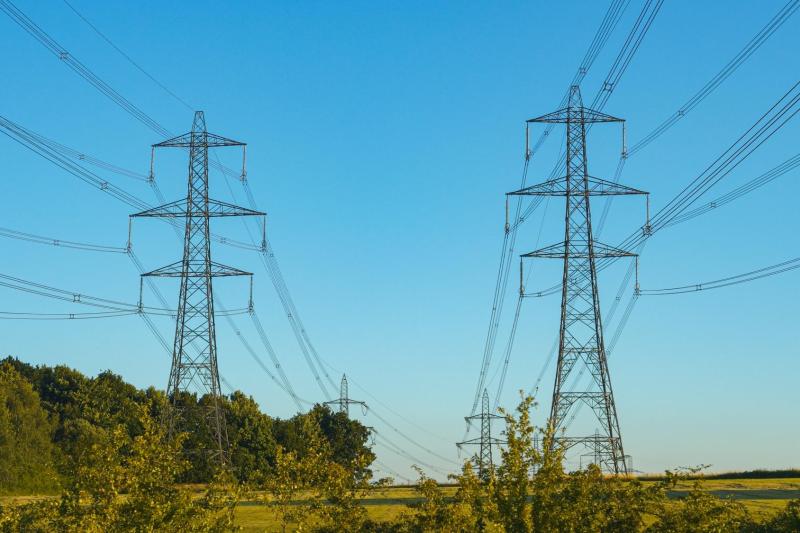
Vlaanderen maakt werk van flexibele aansluitingen
Op 14 juli gaf de Vlaamse regering haar tweede principiële goedkeuring aan het decreet ‘flexibele aansluitingsovereenkomsten’. Een belangrijke stap om flexibele elektriciteitsaansluitingen voor bedrijven mogelijk te maken op het distributienet en het plaatselijk vervoersnet in Vlaanderen.